Station Index
This is a user role protected page.
Please use our Tips and Tricks page for understanding how the SkySuite portal works and how to navigate faster and easier.
Contents
Summary
A station is an Organization that provides flight or passenger services to an airline at an airport. This includes caterers, cabin cleaners, and other ground handling service providers as well as passenger lounges and ticketing agencies. In order for a Station record to exist, there must first be an Organization and OrganizationSite to which that Station can be linked.
Create organization
Organization refers to the company as a whole e.g. Lufthansa, Gate Group, or Coca-Cola, underneath the Organization there can be multiple OrganizationSites (see below). In order to be linked to a Station, the Organization type must be "Caterer/Service Provider". First, please check if the Organization already exists in SkyLog. Here you can find the list of all Organizations [link]. If the Organization already exists please move to the next step. Organizations are centrally controlled and maintained to avoid duplicate organizations being created across multiple operations, therefore if the Organization does not exist contact a Global Administrator or raise a support request. [For more details about Organizations click here]
Organization Sites
An Organization site represents a physical location from which the Organization operates, the site record contains the physical address of the location as well as the main site contact details and the timezone of that site. The site record must exist before you can create a Station record or for that matter any other supply chain participant type such as AirlineSupplier, Warehouse, etc. Firstly Please check if a site is already created in SkyLog with the same address and linked to the same Organization, it is important not to duplicate organization sites. [For more details about Organization Sites click here]
Stations
The station setup contains specifications of that station's operations such as the frequency it should report inventory of airline-owned items and a list (StationItems) of the airline-owned items it needs to provide the services to the airline. Against each item, we record the par levels e.g. how many days of inventory to hold, the frequency of replenishment, the replenishment source and lead time, etc. SkyLog allows you to define at the station level many parameters to customize stations processes. For example, automatic stock count approvals, different ways of RMA management, and the level of automation within process flows.
Stations creation
To create a station record a few things are required to be confirmed: station setup, Supply sources, You can start creating a new station by going to Reference Data/Airline Participants/Stations
SkyLog allows advanced customization of the station processes. To deliver the most productive setup please consult the guide below which explains each customization option on the page
Field |
Description |
Station Site |
Link to Organization site. It is the source of the Station address that is printed on invoices, transport bills and communicated to 3rd parties |
Airport |
Every station must have link to the airport it services. If a single OrganizationSite serves two or more airports then you should create a station record for each airport served. |
Service Type |
Assign relevant station type, e.g. "Caterer", "Airport Lounge", |
Active |
It is a yes /no field that can only be active once all the requirements have been sent up. |
Valid From |
Date of start of operations. |
Valid To |
Date of station closure. If not known or open ended leave blank. |
Station Provisioning Manager |
The person who will be responsible for the provisioning/replenishment of goods for the station (i.e. who will approve requisition requests, inventory reports, etc.). This will be a person within the Airline or the Airline's 3rd party Control Tower |
Person Responsible for Counts |
The person to be assigned (from users registered in SkyLog) who will be responsible for stock counts, this will be someone within the organization of the Station. The selected person will be the recipient of related notifications such as reminders to count, shipment notifications and various escalations/alerts regarding Station Provisioning and Inventory Management |
Is Station Independent from Skylog? |
Station exists within Skylog but is not expected to have any interactions via the UI (Portal)with Skylog – if the station will raise requisitions in SkyLog and/or be expected to submit inventory reports then this setting should always be set as 'No'. Typically this will only be set to 'Yes' if the Station uses their own systems to submit inventory counts and place requisitions and there is an interface between that system and SkyLog |
Automatically Generate Requisitions? |
Yes/No field will either allow (if yes) to generate automatic requisitions after a stock count, via schedule or even manually. If no, only manual orders are allowed to be placed by station. Setting to No is more common for lounges. |
Include Non Orderable Items in Requisitions |
Typically, Skylog only permits 'current' materials to be requisitioned. However, some users prefer to see all materials on the requisition so that they can make informed judgements, including temporary materials which may have been supplied in the past in place of a regular material (e.g. substitute materials where the station par level status = "Temp/Sub"). If the station wishes to see such temporary/substitute items on requisitions then this configuration flag should be set as 'Yes', otherwise, set as 'No'. This setting is often enabled for stations for SAP-Centric clients. |
Generate Automatic Requisitions Upon Count Approval |
This can only be set to "Yes" if "Will Requisitions Be Automatically Generated for This Station?" is also set to "Yes". If set as "Yes" then Skylog will create a new automatic-requisition when an inventory count is approved - this relies upon station par levels being configured for event-driven requisitioning though. If you would prefer that automatic-requisitions are triggered for this station based upon an automatic schedule cycle* then this setting should be configured as "No". * - If you do wish to trigger automatic requisitions based upon an automatic schedule then "Will Requisitions Be Automatically Generated For This Station?" should be set as "Yes" and each material to be included (for automatic requisitioning) should be set as Schedule-driven requisitioning - if set as such, you will be prompted to provide a next requisition trigger date; such configuration is achieved via the station par levels for this station. |
Keep Back Orders? |
When a new requisition is processed should Skylog retain existing back-orders? If Skylog should discard open back-orders upon processing a new requisition, set this configuration flag to 'No'. Otherwise, if Skylog should leave the decision as to whether a back-order is cancelled or processed to a member of the operational team then set this configuration flag to 'Yes'. |
Confirm RMA Shipments? |
If the configuration flag is set as 'No' it is not necessary for the station to confirm the despatch for a RMA. If the configuration flag is set as 'Yes' then the station returning the goods must confirm the despatch. |
Automatic Requisition Negative Numbers Default to Zero |
If Skylog believes that the station has too much stock, it will suggest a negative order quantity in the requisition. If the station does not wish to return such goods, then the requested quantity should be set as zero – meaning that the line/position will be ignored by Skylog. With this configuration flag set as 'Yes', Skylog will automatically set the requested number from a negative value to zero. If this configuration is set as 'No' then the requested quantity will always default to suggested order quantity (even if the suggested order quantity is less than zero). |
Enforce RMA Qty |
If Station is allowed to issue a RMA for parts they haven't ordered from inbound flights etc. then set to 'No'. If 'Yes', the Station will be allowed to return only that stock qty that they counted in the last stock count. |
Receipt Configuration |
The default expectation is that stations will always receipt-confirm all inbound transactions (station orders, direct purchase orders, station-to-station transfers etc.). If however it is permitted for some transactions to be 'automatically' received (i.e. without user interaction), then this can be configured via this setting. |
Should Skylog Consider External Target Quantity Data in Core Functions? |
Specifies whether or not external target quantities, commonly known as FOS + BUS values (supplied to Skylog via uploaded SCA files), will be used by Skylog to affect various Skylog functions. Such functions would include the calculation of the suggested order quantity figure for automatically generated requisitions. The target values will also be used to determine if a material on a submitted inventory count would be flagged as a query or not. If this setting is set as 'No' then Skylog will use the traditional formulas (which won't use target quantity values). If this setting is set as 'Yes', Skylog will consider the target quantities in its calculations. |
Station Depot |
A unique code that identifies the specific station (unique across all airlines). |
Station Loading Code |
An alternate station identifying code which is used by third-party systems to identify a specific station. This code would be used in data files originating from those partner-systems, such as the Service Rules interface EDI. If this interface is used by the operation associated with the station then the uploading and offloading stations identified within the service rules data must correspond to the Station Loading Codes held by Skylog. |
Customer Code |
This is an optional property and should be left blank/empty, it serves a special purpose for a handful of specific catering facilities but has no relevance for the majority of stations and thus can be ignored. |
Default Loading |
This is a mandatory field that may be used when SkyLog generates a forecast for the airline; it can be set to Yes or No (true or false) and it will be used if there is insufficient pre-set data or rules to determine the loading or unloading station. The SSIM (Flight Schedule) file that we receive and process for the airline only tells us the departure and arrival ports for each flight in the schedule. Some ports will be setup with multiple catering stations at a given port and we will determine which station loads and unloads the content of any provisioning code based on pre-set data in the provisioning rule and/or exchange rules. However if there is insufficient pre-set data/exchange rules to tell us which station will perform the loading/unloading then the forecast will use the default station which is determined by this field. Importantly, there can only be a SINGLE default catering station per combination of Port & Airline (additionally, in case it’s not obvious, the station must be active for the default loading to be set to Yes). |
GL Cost Centre Code |
An alternate station identifying code which is used by third-party systems to identify a specific station. This code would be used in data files originating from those partner-systems, such as the Service Rules. GL Cost Centre field links financial data with customer financial systems. In case a new GL Cost Centre is required to be set up please follow the link for guidance how to [link]. |
Supply Source
Supply sources define which warehouses will be supplying stations with goods and which modes of transport are used. It is possible for stations to be supplied by multiple warehouses and this could be defined at the item level in Station Item / Par Level tables. Multiple modes of transport could be assigned for each supplying warehouse with different transportation and handling lead times and a priority ranking to determine the preferred mode of transport.
The Supply Sources button is found in the Reference Data/Supply Chain Participants/Stations. Select desired station by clicking on . At the bottom of the new page will be File:SupplySourceButton.
Add Warehouse
To add a warehouse that will be supplying station:
Add Transport Methods
- Under the Warehouse-Station Link, next to set up warehouse select
to expand the field as per below and select
to add mode of transport from selected warehouse.
- Select accordingly
- Method of transport from drop down list. Note that there are more options then seen on the screen, use scrolling down option to see all modes of transport available.
- Preparation time – days it takes the warehouse to pick and pack.
- Transport duration – days it takes from dispatch until station receipt.
- Rank – priority / default option.

Complete table should look like this.
Station Count Category
Station count categories define which items are counted by the Station and how often they are counted. It also allows you to set the tolerances between expected and actual count quantities (count variances) at which a count line is set to "Query". The level of automation in the count and approval process and also be set – some counts can be set up as auto accepted after they are submitted, a useful feature for stations like lounges with little turnover. Station Count Category can be found under Daily Activities/Inventory Counts/Station Count Categories.
- Select
in the Station Count Categories page
- Select station requiring new station count category
- Review Required - will request that the Station Manager does a full review of every stock count submitted by the Station for this count category, even if there are no lines on the count that are flagged as outside of tolerance
- Auto-Approve When No Queries - stock count will be automatically approved by the system if all count lines are within the defined tolerances (i.e. no queries were generated by the system.
- Auto-Approve Regardless - this will mean that even if there are lines on the count that are flagged as being outside of tolerance, the count will automatically approve - the station provisioning manager will not be alerted and will not need to review the count, thus there can be no re-count process.
- Approval NOT Required - only select this option for "special" counts which are additional to the regular counting cycle, such as a co-ordinated global stocktake

Field | Sample | Description |
---|---|---|
Count Category Description | Full | Description of the count category. The station could have multiple counts with different parts under each, so naming of the count category is useful to avoid confusions. A typical example might be to set up a count category called "Major Equipment" for all technical equipment such as Trolleys/carts or to have a category "Disposables" for all disposable items. |
Count Schedule Option | Automatic Schedule | There are 3 options "Automatic Schedule" (repeats based on provided frequencies), "Manual Schedule" (follows manual dates listed in manual schedule table on the bottom of the page) and "None" (stock counts generated only manually) |
Automatic Schedule Options | Specific Day/s of the Week | You can pick between days of the week or days of the month, days of the week or days of the month [that new inventory counts will be due] |
Specific Day/s of the Week or Month | -- | tick/specify days when stock count should be triggered; if specifying days of the month, each must be comma-separated. Note: you can not specify consecutive days; there has to be at least one day's gap between inventory counts [it's not allowed to instruct a station to perform a new count each and every day |
Weeks Between Counts | 1 | Number of weeks between counts (if 'Automatic Schedule Options' = "Specific Days of the week", rather than Specific Days of the Month) |
Notify Days | 3 | Number of days the stock count will be generated before the expected count date, the station will get an email notification at when the count is generated and then has the notify days to prepare for the count. |
Next Count Generation Date | September 28, 2023 | Select next/first stock date for a count to be scheduled. This date is automatically updated each time a count is generated but a user can re-sync the schedule by editing the date |
Value Tolerance for Count Variances | 100 | Not mandatory, select variances in value per line to tolerate as ok. Meaning if, for example, there is a 100 GBP tolerance and the discrepancy from the expected stock count is 99 GBP, the count will appear as ok. Different tolerance levels can also be set at the item level and the count category tolerance will only apply if there is no item-level tolerance defined. |
% Quantity Tolerance for Count Variances | 10 | Not mandatory, select variance in quantity % per line to be tolerated from the expected count. Meaning if, for example, there is a 10% tolerance and the discrepancy from the expected stock count is 5%, it will not appear as a query. Different tolerance levels can also be set at the item level and the count category tolerance will only apply if there is no item-level tolerance defined. |
Person Responsible for Counts | -- | Select the person (out of those assigned to this station/organization site), that will be responsible for counts and will be receiving notifications related to it. Leave this field blank if you would prefer alerts to be sent to ALL points of contact associated with the station. If no point of contact can be found, alerts will be sent to the station provisioning manager (in lieu of being sent to caterer / groundhandlers with links to the station). |
Include Floating Qty | Yes | Float stock represents the stock that is in the inbound, outbound, and production areas of the station often known as "WIP" (Work in Progress), it does not include stock that is in a storeroom/warehouse area of the Station. If selected "Yes", columns will appear on the stock count page to count both Backup stock and Float stock and report both quantities separately. Backup stock is the stock in a storeroom/warehouse area). If selected "No" then only the Backup stock is expected to be counted and reported. |
Include Breakages | No | If yes, will add a column for breakages to be filled by the Station during the stock count. This reflects any losses at the station since the previous count as a result of breaking/damaging products (to an extent they can no longer be used) - e.g. cracked glass, chipped chinaware, etc. |
Attach Count Sheet File When Notifying Station | Yes | Advise selecting Yes, which will attach an excel file to the notification email, that when filled could be uploaded to SkyLog for submission. It is a good tool to avoid manual entries in the portal. Note, for new airlines, additional setup is required to enable this - please raise a support ticket and ask for this option to be enabled though. |
Consumption Trend Span (Days) | 180 | Default value is 180, and if left blank it will generate a value of 180 days. This value is used in the calculation of the "smooth" average past daily consumption, if set to 180 it will look at the last 180 days when calculating the daily average but it can be set longer or shorter. |
Generate Automatic Requisitions Upon Count Approval | Yes | If Yes, the system will generate an automatic requisition after the stock count is approved (although this is dependent upon the station itself being configured to support automatic requisitioning too). |
Include All Items in Automatic Requisitions | Yes | Yes, will include all active items in any auto requisition (even if the suggested order is 0) |
Delay (Hours) For Automatic Requisition Generation | 0 | This is the number of hours after count approval before which any automatically triggered requisition should be triggered |
Include All Station Par Levels In Counts | No | Only select YES for "special" counts which are additional to the regular counting cycle, such as a coordinated global stocktake. Thus for regular counts, this setting should be set as NO. Only count categories where this configuration setting is set as NO will appear as a valid option when defining a default count category (See 'Station Defaults' section below). |
Update Station Par Levels | Yes | Only select NO for "special" counts which are additional to the regular counting cycle, such as a coordinated global stocktake. So for regular counts, this should be set as YES. Only count categories where this configuration setting is set as YES will appear as a valid option when defining a default count category (See 'Station Defaults' section below). When set as YES, assuming that the count is approved, the approved inventory figures will be copied across to the station par levels and will be used as the starting inventory figures for the next iteration of the count. Additionally, with this configuration flag set as YES, it will also mean that average consumption figures are calculated and may have a bearing on RMA functionality too (depending on station-level configuration tho). |
Count Auto Approval Option | Review Required |
NOTE: You can only select the 'Approval NOT Required' option when the 'Update Station Par Levels' flag is set to 'No'. IMPORTANT: Be warned, this is the final configuration flag when you add or edit a station count category record, if you select this option, you will find that it will toggle (update) the settings for "Include ALL Station Par Levels" and "Update Station Par Levels" - so you may find that your resultant count category is not as you had originally specified it because of this final setting. If you want regular (standard) counts to always sail through, skipping the approval step then choose the "Auto-Approve Regardless" option instead; thus, the station provisioning manager won't be notified to review the count when the caterer has submitted their inventory figures. |
Sample of complete Station Count Category setup
Station Defaults
Station defaults are used whenever doing a mass creation of Station Item records, for example - when copying the items from one station to another, or when the forecasting system, as a result of loading or flight schedule changes, creates new items for that station. The criteria in station defaults will be applied to all items copied or created from forecasting but can be edited item by item as required.
- In the Stations page (Reference data/Supply Chain Participants/Stations) select a station in edit mode.
- Fill Station Default table accordingly. Table with descriptions is presented below
Stock Items / Par Levels
Station Par levels refers to items a Station would be allowed to place orders for and receive into stock. These can be created in a few ways: copy Par Levels from identical/similar station or do it one item at a time
Copy Par Level from existing station
- in Station Par Levels select a stations you want to copy whole par level from
- At the bottom of the screen press the button "Copy"
- In field “Use Destination Station Defaults?” mark to “Yes”.
- Select station you want to copy par levels to.
- Confirmation screen will appear.
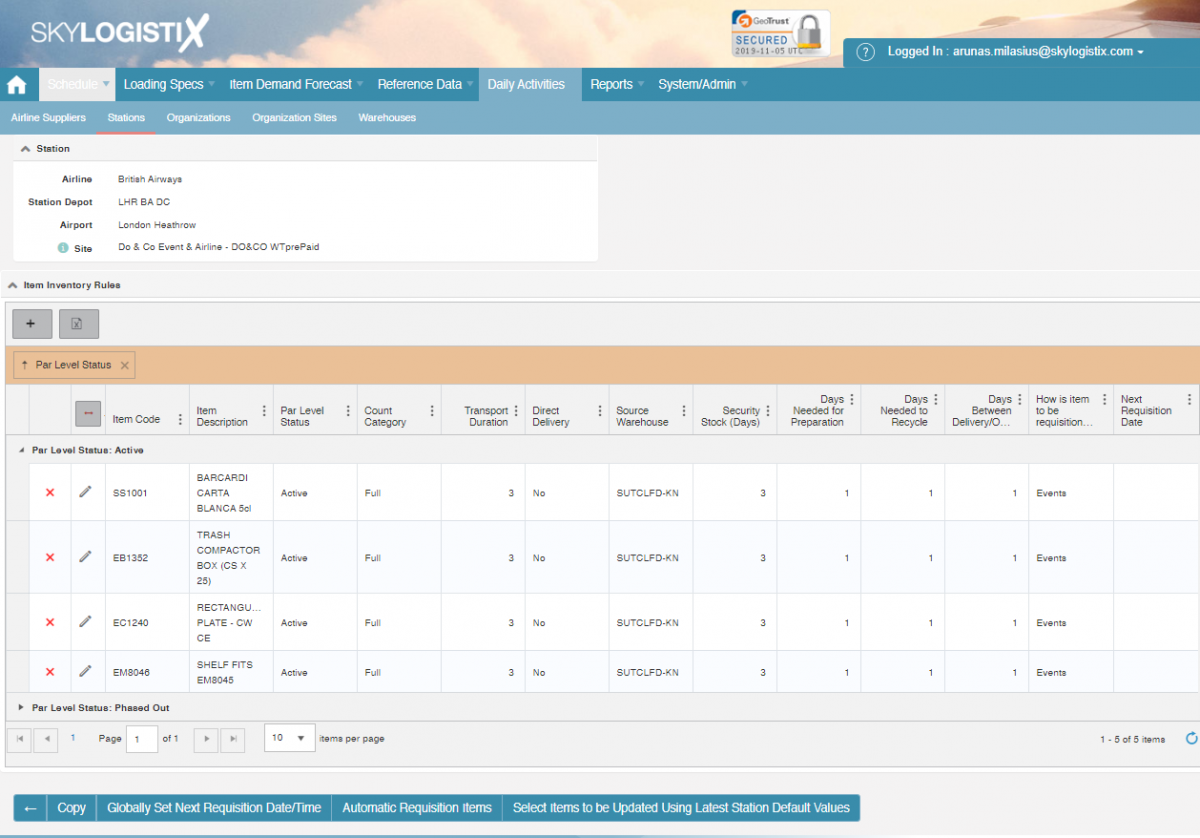
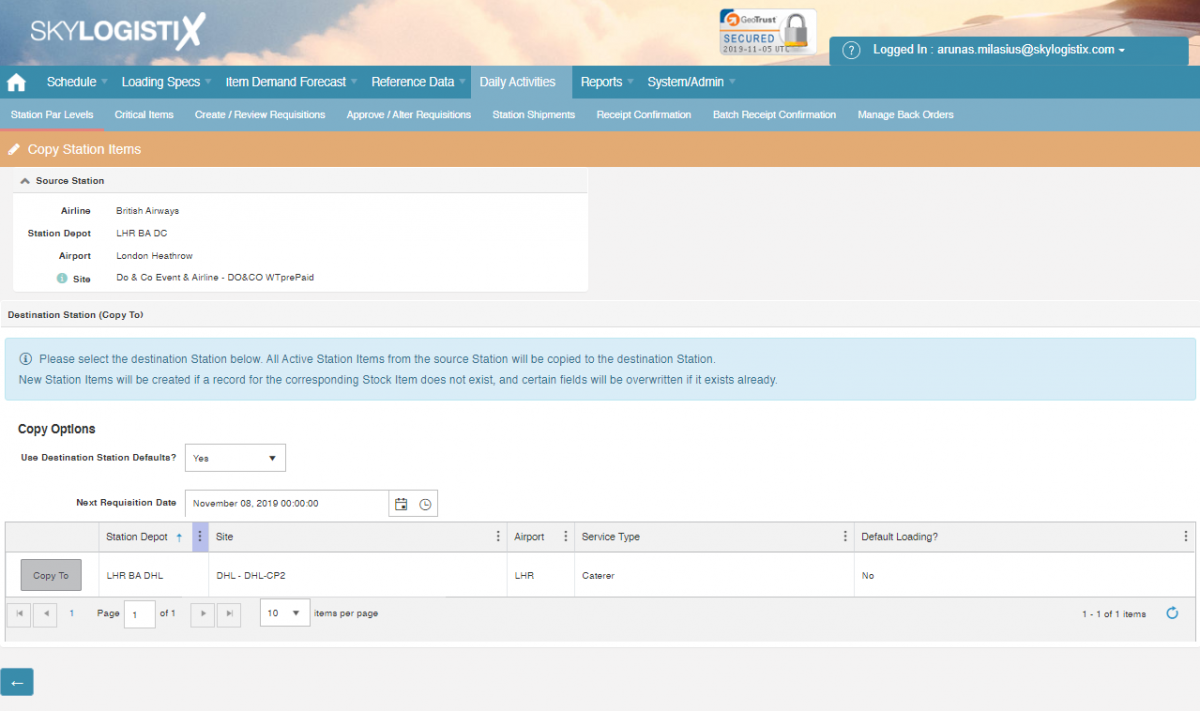
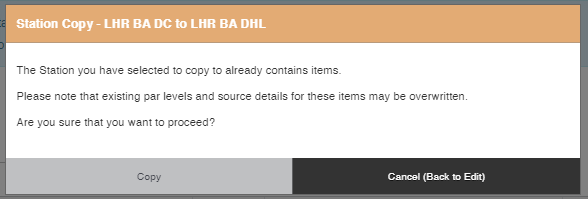
Adding Items to Par Levels
Station Par levels are available for review and edit under Daily Activities in Provision section. Please select the Station with . To add a new item press
and complete filling in the table to finalize the setting up, make sure that the item status is marked "Active" on the bottom of the page.
Closing Station
In order to close an active station, prior to marking the Station as not active, few very important steps need to be taken to make sure the MRP forecast is reflected correctly for material planners, and that all the assets are accounted for, the below steps need to be taken;
Stock In transit is accounted for
Any stock that is in transit to the Station needs to be receipted and moved via RMA to another location (another Station or Warehouse), used up at the station, or scrapped with a scrap order. There should be no stock left at the station before the station can be closed
Station Stock Counts are closed
All station stock counts need to be closed, and most importantly, the last stock count needs to have all items showing zero - the last stock count qty of each item needs to be 0. This is important to reflect correct consumption and asset valuations.
End of the forecast
Any manual forecast uploaded in SkyLog related to the Station you want to close needs to be removed from SkyLog.